How to Utilize and Understand our Job Status Screen
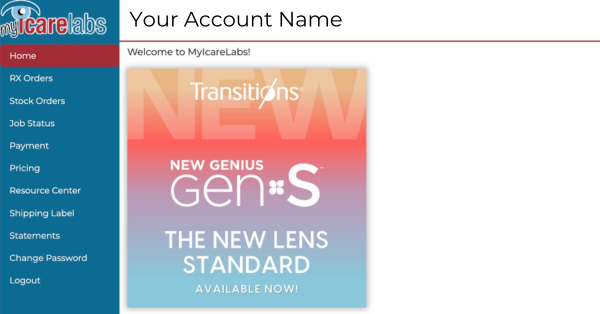
In our ongoing quest to always be America's easiest lab to work with, our amazing customer portal provides all of our customers with 24/7 access to everything they need. This includes Rx ordering, payments, statements, and more. One of the best features available is real-time job tracking as your work is going through our lab! This blog will explain the various codes you'll see on the job status screen and the estimated turnaround time.
First and foremost, please keep in mind that the following turnaround times are all estimates that skew towards the high end so we can set realistic expectations for you to help set those for your patients. Surfacing prescription lenses is a complex process with numerous quality control features used to prevent bad jobs from leaving the lab. Unfortunately, that also means that some jobs can take longer than others if they fail QA or take a breakage for any reason.
Our lab team tracks all jobs and we have turn-time goals for all categories of jobs. The exciting news is that we hit these goals on over 90% of the jobs that flow through our lab. For uncoated uncut lenses, the average process time is under 24 hours from the time of order. AR coated uncut jobs average just under 48 hours. For finished work, the timer starts when we receive the patient's frame. Finished uncoated lenses average under 48 hours while finished with AR is just under 72 hours.
Jobs In Progress
After logging into your myIcarelabs account you can select "Job Status" in the blue menu on your left. This will take you to the "Jobs In Progress" tab. From here you will see all of your work in chronological order going from your most recent job back to your oldest job that is still processing.
You'll have your job ID, patient name and ICL number, status, status date, and available actions. By clicking on the blue job ID link you'll see the full order details which will include the complete Rx, material, and all job order information you provided to us.
On the far right under the actions section, you'll usually see one or two options here. Those would be "copy job" if you need to restart a new job for the same patient using the same Rx information and "hold job". Once you click "hold job" you'll be asked to enter the reason to hold the job which would allow you to update instructions for the job.
This is a useful feature if you realize you need to add AR to the job after you hit submit but don't want to enter all of the information in again. Please keep in mind that depending on where your job is in process we may not be able to update it as requested. If your job is already in the AR chamber and you are requesting we change the Rx that just simply isn't possible since the lenses have already been surfaced.
Status & Status Date
Under the status, you will find the current station in the lab that particular job is at. The status date will give you the last date and time it was scanned. These are all updated in real-time on your account. We have a fully staffed second shift that is processing work here till around midnight or even 1 am on some nights. Please also keep in mind that we do not work on the weekends so work is processing Monday through Friday.
Here are all of the statuses you may see on your jobs' journey through our lab.
Order Entry
Your order is in the system and has now started processing. If the job is for uncut lenses and we have the lens blanks in stock then your order will begin processing. If this is a frame-to-come order then we do not start processing the lenses until we receive the frame so you will see this status until the frame is received.
For jobs that are under this status, you can still use the hold job feature to make any necessary updates to the order.
Lens Department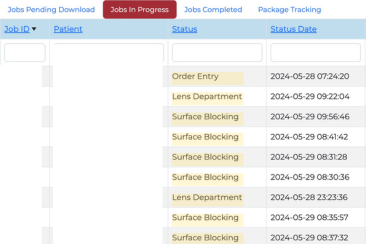
Your job is about to start its surfacing journey in our lab. Lens blanks are in stock and a lab ticket has been printed for your job. Lenses have now been taped and are almost ready to start being surfaced. Jobs with this status can still be updated using our hold job feature.
Surface Blocking
Your job has now been placed on an alloy block which keeps them secure while being surfaced in our machines. This is the last step you can utilize our hold job feature to make any changes to surfacing instructions.
Surface
Now here is where the fun begins! Your lenses are being surfaced with our state-of-the-art generators which grinds the patient's Rx into the lenses. After that, we polish the lenses, and then our laser engraver etches the lens identifier markings and tray numbers into the lenses.
Backside Hard Coat
We're proud to provide industry-leading scratch spin coating. Lenses receiving a backside hard coat or spin coat will receive them during this step.
Quality Assurance (QA)
At this step, the lenses are checked for correct prescription and to verify no defects are seen. If the job is for uncut lenses without AR then they will be shipped out to you now. For jobs with AR or finished jobs, they will move on to the next steps in the process.
AR Coating
Lenses needing anti-reflective coatings will now head over to our world-class AR chambers. This is an extremely involved process, but essentially the lenses will be washed to clean off any leftover debris. Then they are added to our AR chamber to receive the chemical anti-reflective coating on the lenses.
Quality Assurance (QA)
The lenses have now headed back from our AR room back to the main lab. Here they are checked for AR defects and spot-checked for power. If the lenses are uncut and pass inspection then they are now ready to ship. For complete jobs, they now head to our finishing department.
Frame Department
Now the lenses are being matched up with their frame. From here, our seasoned team of finishing experts will prep the lenses for edging. After that is complete they mount the lenses into the frame.
Quality Assurance (QA)
Now your finished job is ready for a final inspection. If it passes inspection then it will be shipped out.
Jobs Completed
Now that your job is done and shipped, you will find it under the "Jobs Competed" tab to the right of the "Jobs In Progress" tab. Here you'll be able to pull up old jobs as well as utilize our revamped remake/redo system if needed. Jobs listed here will go from your most recent completed job all the way back to your first order with us.
For jobs that are marked as "shipped" after 4:30 pm Eastern, they will be mailed out to you on the next business day.
Don't forget, we are just humans working with machines at the end of the day. Even with our amazing team trying as hard as they can, mistakes do happen which can cause delays. We have several steps in our process that attempt to minimize this as much as we can but it is possible to see jobs go through the same steps more than once if they fail QA.
Restarting those jobs is an automatic process with nothing needed on your part. We automatically prioritize these jobs to get them out the door to you as fast as we can. Fast jobs don't count for much if they aren't correct! We pride ourselves in some of the lowest error rates in our industry. Our President and the operations team lead a weekly meeting every Monday with our team going over our numbers for every department to ensure all of our staff is on the same page so we can provide you with the highest quality lenses.