Why We Crib Lenses
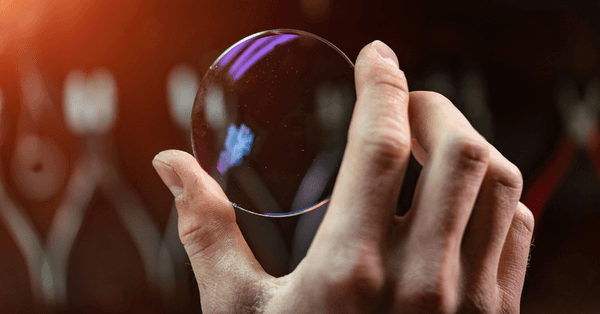
In today's modern lab with digital processing and the high percentage of jobs being processed with non-glare coating, cribbing has become the norm. While many might be used to receiving cribbed lenses, I would figure that some do not understand why.
Cribbing is simply the process of reducing the circumference of a semi-finished blank. With today's digital generators, this is done in a matter of a couple of seconds during surfacing. Crib size is based upon measurements we either take for finished work or measurements supplied by our customers for uncut jobs. We will come back to this a bit later in this blog.
What are the benefits of cribbing lenses?
There are four main reasons for cribbing.
- Helps create a better and cleaner backside surface
- This is very important for lenses with non-glare coating as AR coating allows more light transference which a poor surface could negate
- Non-glare coating by design will show even the smallest of surface imperfections
- Speeds up process in both surfacing and finishing
- A smaller blank size requires less time during polishing
- Having to edge a smaller blank will speed up edging time
- Creates less spoilage
- Smaller blanks tend to coat better which decreases hard coat and AR coating defects
- Less pressure while edging which will reduce slips and spins while finishing the job
- Reduces wear and tear on finishing equipment
- Lenses edge faster and with less drag adding life to edging equipment
Like almost everything else that has great benefits, there are a few drawbacks to keep in mind.
You will be working with smaller blanks which require more precise measurements. To help ensure proper cut we have added some features to our website over the last year. Utilizing these will help with cutout on all jobs and give you better thickness on your plus jobs.
When placing your uncut orders, you will want to follow these three steps to ensure you receive the proper lens blank sizing.
- Ensure you have the proper frame measurements: Measure your frame by hand instead of using the manufacturer's measurements.
- Input the frame name and model number: We have recently expanded our frame database and stored the tracings of frames in our system. When you input this information, the system will grab the frame information that is stored and use the tracing for reference versus a generic, unknown shape.
- Choose a frame shape: After you have done steps one and two, you will want to select the frame shape that best fits the frame at hand. While we continue adding frame information to our database, we may not have the unknown frames, so it is important to select the appropriate frame shape.