How To Get Less Remakes From Your Wholesale Optical Lab
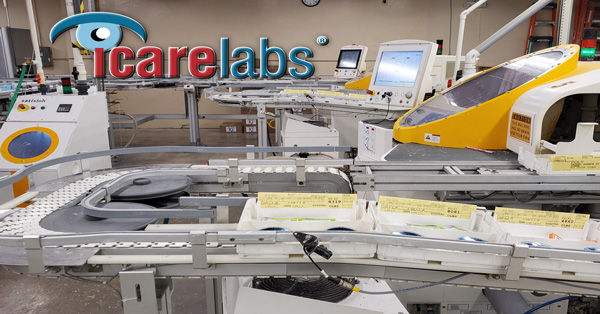
In the relationship between the lab and the optician, nothing is more agreed on than the aggravation of redoes and remakes. No one wins when a job has to go back to the lab to be redone.
Above all else, the patient has to experience a delay in receiving their new glasses. Often these delays can harm your reputation as an eye care professional. When the delay goes on long enough it could cost you return business and even force a refund and lost sale.
Remakes also cost you time, you've had to check in a set of lenses and edge them just to find out that there is something wrong. Then you have to take time to reorder. For us at the lab level, we have to run the job back through the lab for no charge. This costs us labor, wear and tear on our equipment and hard dollars for a new set up lens blanks.
With this knowledge, we always strive to make sure what we ship out is correct. The only thing that is worse than a single remake is doing the same job over and over again. The machinery in our state-of-the-art wholesale optical laboratory that we use for surfacing your work is very accurate. When we do a remake with the same information going in, it will most likely turn out the same.
There will always be a job or two that have to be remade. As good as the equipment is there are still human beings on both sides of the job. Mistakes are going to happen. What we can control, more often than not, is how many times a job goes back through the lab. We would all agree that a remake on its fourth time through the lab, being 3 weeks old, is one of the worse things for everyone involved.
After years of doing what I do, I have learned that thickness issues on uncut lenses and patients not being able to see well lead the pack in multiple remakes. Here are some tips to help us get these jobs correct on the first time through or at least on the first remake.
Lens Thickness 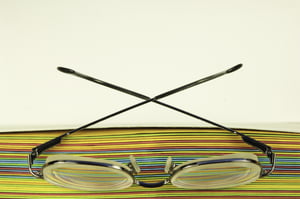
To start with, most thickness issues can be avoided by supplying us with just 3 things: accurate box measurements, base curve, and a shape number. Our online ordering system at myicarelabs.com gives you spots to enter the A, B, Ed, and DBL. Give us accurate measurements; a guesstimate just will not work. On plus lenses, the base curve is paramount. Take time to find what your patient's current glasses read and request a match to this. We do not charge extra for this.
If you are ordering uncut lenses please take time to utilize our shape number chart. This can be found on the drop-down at the very top of the order page. Select “uncut" for the job type and then select the shape "#" this will allow you to open up a PDF with 17 different shapes.
While using all of the above information, it will cut way down on thickness and cut out issues. What do you do if you receive a job off on thickness or cutout?
As I mentioned above, ordering once again without making changes will not work. You will most likely receive lenses back that are the same as the original. If you receive an uncut order with a thickness issue please call in your remake.
On minus lenses
Please have an accurate center thickness ready for us before calling. Please keep in mind – if the CT is below 1.4 on Poly and 1.8 on all other materials, remaking will not help. We often get an order for a remake in high minus based upon the cosmetics after they have been edged. If the center thickness is correct, remaking will not help. This might be the best that it could be based upon frame size and decentration.
On plus lenses
Please go ahead and edge the lenses. Unlike the minus lens where the center thickness is key, we need to know what the thinnest point on the edge is. Once again, we will be shooting for a thin edge measurement of around 1.4 mm. Have this information ready for us so we can help in making sure the remake comes out with the correct thickness.
Often thickness issues are more of a result of poor frame fit and base curve than actual thickness issues with the lenses.
A patient can’t see well with new lenses
While this is not that common, we do have remakes for this. Once again, this needs to be addressed and researched before remaking.
Let’s layout a scenario – you have just hung a new pair of glasses on a patient and they do not seem happy with their vision. What do you do?
- Find where the visual issues are – near, intermediate, distance
- Check the fit of the frame making sure everything is aligned
- Check the power in the lenses once again (this should have already been checked before)
- Does the base curve on the new pair match the old lenses?
If all of this is good, markup lenses and make sure that progressive fitting cross or OC is on the pupil.
Have the patient try them for 48 hours. Adaptation takes time with new lens designs and/or new Rx.
If all checks out and the patient is still having issues after wearing them for a couple of days, give us a call. Have the information above ready for us to review with you. This will help your account manager in their next step decisions.
By following these easy to follow steps, we can avoid long delays in getting your patient a great pair of quality eyewear. Nobody wins when a set of lenses churn over and over through the lab. Not all remakes are created equal. Please utilize your account manager to help with these issues.
By working together, we will save all of us time and money. Most importantly, we might just save your sale and send a satisfied customer out your door who will come back and see you next time.